Auditing Quality Management Systems: A Guide to Ensuring Excellence
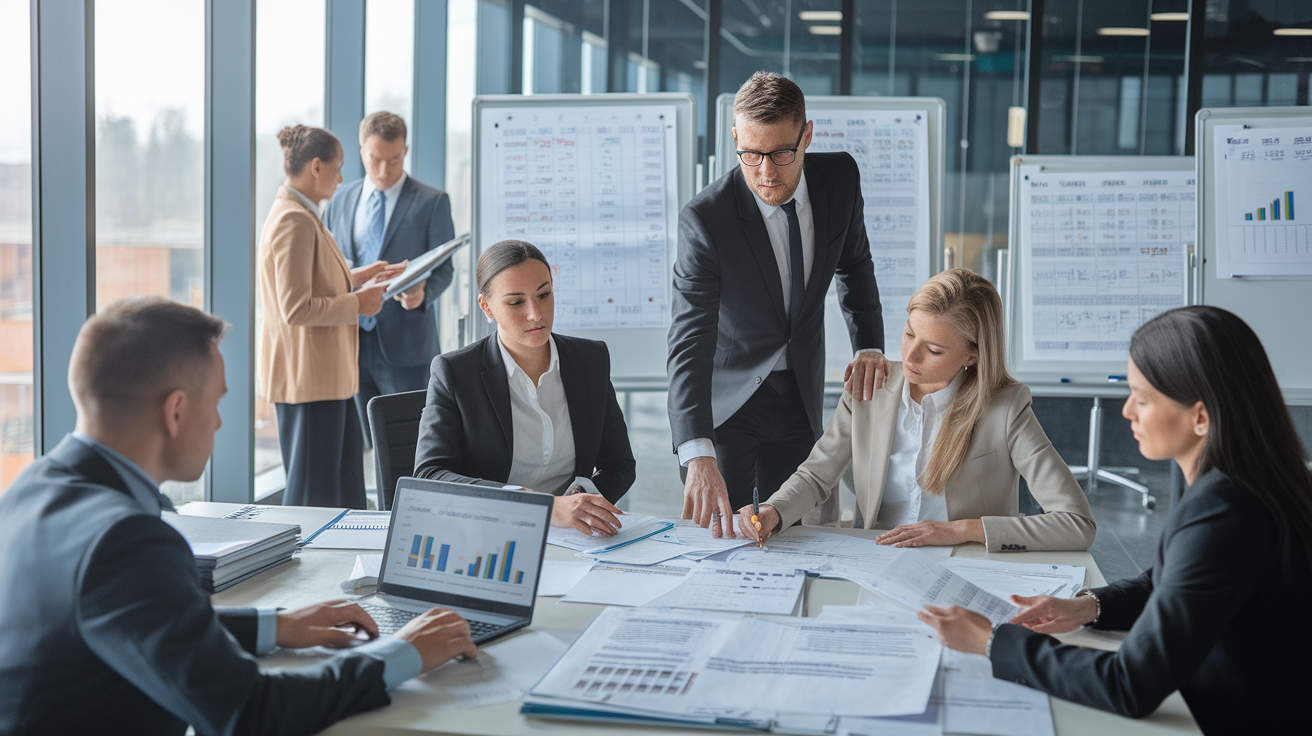
Maintaining high standards in goods and services depends much on quality management systems (QMS). Regular audits, however, help these systems to produce the intended outcomes by means of their absence. By means of audits of QMS, companies can find flaws, guarantee compliance, and propel ongoing development.
The main features of auditing a quality management system will be discussed in this paper together with their relevance, procedure, best practices, and common difficulties.
Why Auditing a Quality Management System is Essential
A well-executed QMS audit helps organizations achieve:
✅ Regulatory Compliance – Ensures adherence to industry standards such as ISO 9001, Six Sigma, or other regulatory frameworks.
✅ Process Optimization – Identifies inefficiencies and areas for improvement, leading to streamlined operations.
✅ Risk Mitigation – Helps prevent quality failures, safety hazards, and operational risks.
✅ Customer Satisfaction – Ensures that quality objectives align with customer expectations and market demands.
✅ Continuous Improvement – Facilitates a culture of ongoing enhancements and operational excellence.
Types of Quality Management System Audits
Organizations can conduct different types of audits based on their goals and regulatory requirements.
1. Internal Audits
- Conducted by in-house auditors or quality teams.
- Identifies internal weaknesses before external inspections.
- Helps in preparing for third-party audits.
2. External Audits
- Performed by an independent body, such as a certification agency.
- Determines compliance with international standards (ISO 9001, HACCP, etc.).
- Required for certification and regulatory approvals.
3. Supplier Audits
- Evaluates the quality management processes of suppliers and vendors.
- Ensures that outsourced materials and services meet quality standards.
- Helps in risk management and supply chain efficiency.
4. Compliance Audits
- Focuses on adherence to industry-specific legal and regulatory standards.
- Conducted by regulatory bodies or internal compliance teams.
- Ensures the company operates within legal frameworks.
5. Process Audits
- Examines individual processes within the QMS.
- Assesses effectiveness, efficiency, and conformity to best practices.
- Helps in refining workflows and eliminating bottlenecks.
Say Goodbye to Manual Work – Free Axonator Demo! https://axonator.com/request-for-demo/
Key Steps in Auditing a Quality Management System
Step 1: Planning the Audit
Before conducting an audit, it’s crucial to define objectives, scope, and methodology.
✔️ Identify Audit Type – Decide if it’s an internal, external, supplier, compliance, or process audit.
✔️ Set Clear Objectives – Define key performance indicators (KPIs) and compliance requirements.
✔️ Select Audit Team – Assign experienced auditors with knowledge of quality standards.
✔️ Prepare Checklists – Develop structured checklists based on ISO 9001 or other frameworks.
Step 2: Conducting the Audit
During the audit, auditors collect data, examine processes, and interview employees.
✔️ Document Review – Assess policies, procedures, and previous audit reports.
✔️ Process Observation – Observe work practices, inspections, and quality control measures.
✔️ Employee Interviews – Engage staff to understand their adherence to quality protocols.
✔️ Sampling & Testing – Evaluate product or service samples for defects and compliance.
Step 3: Reporting Audit Findings
After data collection, auditors compile findings into a structured report.
✔️ Identify Non-Conformities – Highlight deviations from set standards.
✔️ Provide Corrective Actions – Recommend steps to address issues.
✔️ Rate Compliance Levels – Use grading or scoring systems for clear assessments.
✔️ Share with Management – Present findings to leadership for decision-making.
Step 4: Implementing Corrective Actions
Organizations must act on audit recommendations to enhance their QMS.
✔️ Develop an Action Plan – Assign responsibilities and deadlines for corrective actions.
✔️ Monitor Progress – Track improvements through follow-up audits.
✔️ Document Changes – Maintain records of all corrective measures.
Best Practices for an Effective QMS Audit
🔹 Adopt a Risk-Based Approach – Prioritize high-risk areas to minimize quality failures.
🔹 Use Technology – Leverage audit software for real-time tracking and analysis.
🔹 Encourage Employee Involvement – Promote a culture of quality awareness and participation.
🔹 Benchmark Against Industry Leaders – Learn from competitors and industry best practices.
🔹 Ensure Auditor Independence – Internal auditors should be neutral and free from bias.
Common Challenges in Auditing a QMS (and How to Overcome Them)
🚧 Resistance to Audits – Employees may fear audits as fault-finding exercises.
✅ Solution: Foster a culture of continuous improvement rather than blame.
🚧 Lack of Standardization – Inconsistent processes make audits difficult.
✅ Solution: Use standardized audit checklists and templates.
🚧 Insufficient Documentation – Poor record-keeping leads to compliance issues.
✅ Solution: Maintain updated records and ensure easy access.
🚧 Failure to Act on Findings – Ignoring audit recommendations weakens the QMS.
✅ Solution: Assign accountability and follow up on corrective actions.
Final Thoughts
Examining a quality management system is a strategic instrument for business excellence, not only a compliance activity. Under proper direction, audits enable companies to reduce risks, increase consumer confidence, and improve efficiency. Following best standards and tackling shared issues helps businesses turn QMS audits into chances for expansion and ongoing development.
Are you prepared to maximize your QMS audit process? Start right now to open the path for operational excellence! 🚀