Challenges & Solutions in Uncured Rubber Recycling
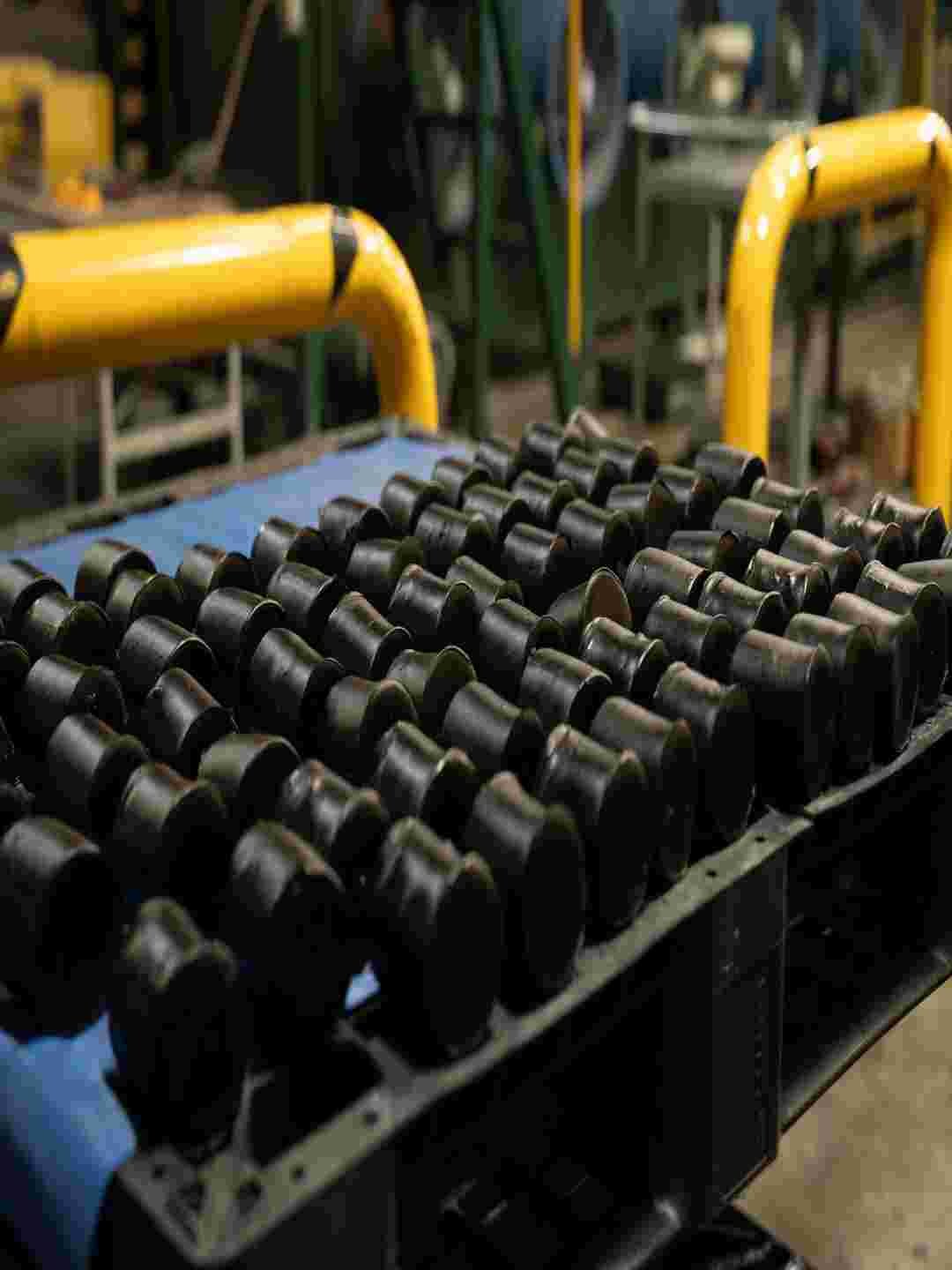
Rubber is an essential material in industries such as automotive and aerospace, as well as construction. Unlike old tires, which are widely recycled, recycling uncured rubbers is not so simple because it poses significant challenges related to the chemical composition and difficulties in processing. Uncured rubber, also called raw or green rubber, has not yet been subjected to vulcanization and is, therefore, more difficult to handle and reuse.
Despite these obstacles, advancements in material science and innovative recycling techniques are helping manufacturers develop sustainable solutions. We will explore the major challenges in recycling uncured rubber and how manufacturers can overcome them.
Challenges in Recycling Uncured Rubber
1. Lack of Cross-Linking Stability
Uncured rubber is highly flexible and sticky because it has not undergone vulcanization, the process that creates cross-linked molecular structures to provide durability and strength. This makes it difficult to handle, transport, and repurpose new products.
Solution:
Cryogenic Processing: Freezing uncured rubber using liquid nitrogen makes it brittle, allowing for easier mechanical grinding and separation.
Pre-vulcanization Treatments: Light curing or controlled pre-vulcanization techniques can enhance stability before recycling.
2. Contamination from Additives and Fillers
Numerous fillers, plasticizers, and chemicals included in raw rubber make recycling more difficult. It might be challenging to preserve material consistency for reuse since these compounds can change the material’s chemical and physical characteristics.
Solution:
Advanced Filtration Techniques: Using solvent extraction or thermal depolymerization can help separate useful rubber from unwanted additives.
AI-Based Material Sorting: Modern sorting systems, including spectroscopy and artificial intelligence, can categorize rubber depending on composition, therefore increasing recycling effectiveness.
3. Difficulty in Processing Without Vulcanization
Uncured rubber doesn’t have the same flexibility and durability as cured rubber because it hasn’t been vulcanized. It might lose its mechanical qualities when recycled, making the new goods less strong.
Solution:
Reactive Extrusion: During recycling, this method changes the molecular structure of uncured rubber, which makes it easier to incorporate into new rubber formulas.
Co-polymerization Techniques: Adding additional polymer components to uncured rubber can make it stronger and more useful.
4. Limited Market Demand for Recycled Uncured Rubber
Recycled cured rubber is used a lot in outdoor areas, road materials, and insulation. But recycled uncured rubber doesn’t have a clear market. A lot of producers like fresh rubber because they know it will work well and be of good quality.
Solution:
Industry Partnerships: Companies that make rubber and companies that recover it can work together to help set quality standards for recycled uncured rubber.
Government Incentives & Regulations: Policies promoting recycled content in rubber-based products can drive demand and encourage manufacturers to use sustainable materials.
5. High Energy Consumption in Recycling Processes
Some ways to recover uncured rubber, like thermal decomposition and chemical breakdown, need a lot of energy, which means that many producers can’t afford to do the process.
Solution:
Microwave-Assisted Recycling: This method uses electromagnetic waves to break down rubber at lower temperatures, reducing energy costs.
Biodegradation Using Microorganisms: Scientists are looking into bugs and fungi that can break down parts of uncured rubber with little energy.
Innovations Driving Uncured Rubber Recycling
1. Devulcanization Technologies
Even though the rubber is not cured, a certain extent of vulcanized rubber may still be conditioned during storage or when mixing. Modern devulcanization methods such as ultrasonic, mechanical, or even chemical methods are utilized for breaking apart the rubber before being reprocessed.
2. Use of Supercritical Fluids
The processing of uncured rubber has been a subject of recent development in the area of supercritical CO₂ use. Supercritical CO₂ is considered the most environmentally friendly solvent suitable for extraction and recycling of rubbers. They are a selective material recycling method without harsh chemicals being an aspect of this technology.
3. Blockchain for Supply Chain Transparency
The use of blockchain technology in rubber recycling is meant to track and authenticate recycled uncured rubber, whose end goal will improve traceability in materials improving the quality standards.
4. 3D Printing with Recycled Rubber
Advanced 3D printing techniques now enable the use of recycled uncured rubber in additive manufacturing, opening new applications in custom parts production.
The processing methods, advanced AI-based sorting of materials, and sustainable energy solutions will make uncured rubber recycling by manufacturers economical and efficient.
As the demand for eco-friendly manufacturing practices grows, investing in Uncured rubber recycling will not only reduce waste but also open new opportunities for sustainable product development.